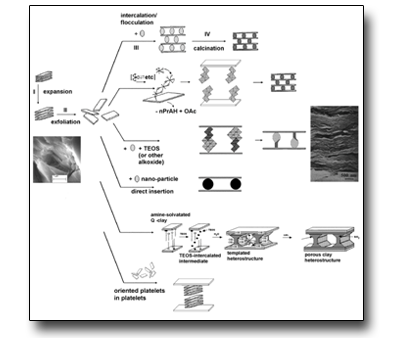
TECHNICAL SPECIFICATIONS
-
porosity: micro (up to 2 nm); meso (up to 50 nm); macro (> 50nm). (porosimeter and equation BJH for PSD)
-
porous volume (t-plot method)
-
porous geometry (absorption hysteresis curves of N2, porosimeter)
-
specific surface area (BET equation or Langmuir, from a few tens up to thousands of m2/g)
-
acidity (pyridine test with FTIR)
-
crystal size (>200 nm) Structure and phases (XRPD)
-
contensts in metals (few units %) (AAS)
AVAILABLE TECHNIQUES
Inorganic porous materials synthesis
- hydrothermal synthesis (Zeolites, zeotypes)
-
or with organic template (shape-directingeffect)
-
or with a combination of different oxides (different tetrahedral atoms for different T-O bond lengths)
-
or with specific spatial units (addition of 4R or 6R units to AlPO)
-
-
Methods of pillaring/interleaving of 2D materials (see figure) (Smectitic clays, group IV metal phosphates, LDH, metal oxides)
-
batch methods (MOF, ZIF)
-
sol-gel methods (Silica-alumina from organosilanes and aluminate gels)
Preparation of catalysts on porous supports - chemical methods
-
Ionic exchange
-
Co-precipitation
-
Deposition-precipitation
-
Microemulsion
-
Saturation by impregnation
Preparation of catalysts on porous supports - physical methods
-
sonication
-
microwave irradiation
-
PLA
Modifications of porous inorganic materials
-
Introduction of acidic or basic function (modification of the Si/Al ratio during synthesis);
-
Introduction of metals into the framework (replacement of Si and/or Al with Ti, Cr, Zr etc during synthesis);
-
Elimination of metals from the framework (post-synthesis dealumination).
Other inorganic materials synthesis
-
sol-gel synthesis of bio-glasses
SAMPLES
- samples of:
-
Zeolites: Y, USY, ZSM-5
-
Zeotypes: MCM41, FSM 16, MCM23
-
PILCs
-
PCH
-
MOF
-
ZIF
-
LDH
-
PILPs
-
Supported metal oxides (ceria, etc)
-
Bio-glasses
-
- samples from 1 to 500g
- samples with fixed metal content
USED FOR
Catalysis
- Depolymerization of plastics (PET, PP) for the recovery of monomers and energy;
- HDO of lignin for the production of fractions for jet fuel;
- Production of syngas from CO2 and H2O (water shift).
Absorption/separation
- Separation and concentration of atmospheric C2;
- Chromatographic separation of hydrocarbon mixtures;
- Absorption of mineral acids from biofuel blends.
CASE STUDIES
Catalytic pyrolysis of polyethylene
Recycling plastics through thermal or catalytic treatments is one of the possible alternative solutions to landfills and dispersion into the environment. The main targets are the production of fuels or the recovery of monomers and/or chemical products.
If a comparison is made between the pyrolysis products of polyethylene obtained through thermal degradation (top in the figure) and catalysis (bottom), it can be seen that the first gives a homogeneous and degrading distribution of products with a carbon atom number from C1 to C24, while with a suitable catalyst products grouped in the range of C12-C23 diesel fuel are obtained.
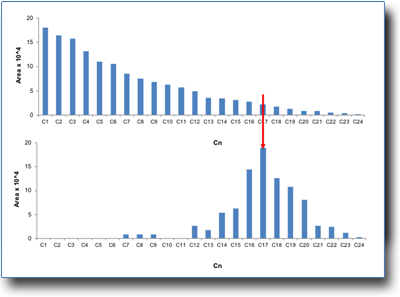
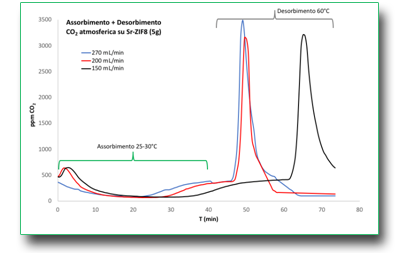
Absorption, concentration and recovery of atmospheric CO2
In the struggle for the reduction of worldwide CO2 emissions, the large plants for the production of electricity and in general the large oil and chemical industries have a sure place in the foreground. The huge quantities of CO2 generated by these plants are, however, easily intercepted before being released into the atmosphere. This, as long as effective technologies at high temperatures are made available, for separating CO2 from other gases with adsorbents capable of capturing large quantities per unit of weight and/or volume. One of the methods in use, which still requires an energy expenditure equal to about 20% of the total produced in a plant, uses toxic amine solutions, through which the effluents rich of CO2 are allowed to pass. CO2 binds to the amine and is thus separated. In order to then recover and store CO2, the amine solution must be heated for its release. However, other techniques are available such as cryogenic and membrane separation, and the utilisation of solid molecular sieves. Among the absorption processes, PSA (pressure swing adsorption), VSA (vacuum swing adsorption) and TSA (temperature swing adsorption) are particularly interesting. For absorbents to be applied to these techniques, the following characteristics are required:
1) high selectivity and adsorbing capacity for the CO2;
2) adequate adsorption/desorption kinetics;
3) constant adsorption capacity even after several cycles in operating conditions.
The experiment in the figure illustrates the absorption and desorption of atmospheric CO2 with a Sr-modified ZIF, using TSA.